What goes on Inside those Crazy Looking StoneWorks Vans?
- Brian Baltzegar
- Feb 7, 2019
- 3 min read
Updated: Oct 15, 2023
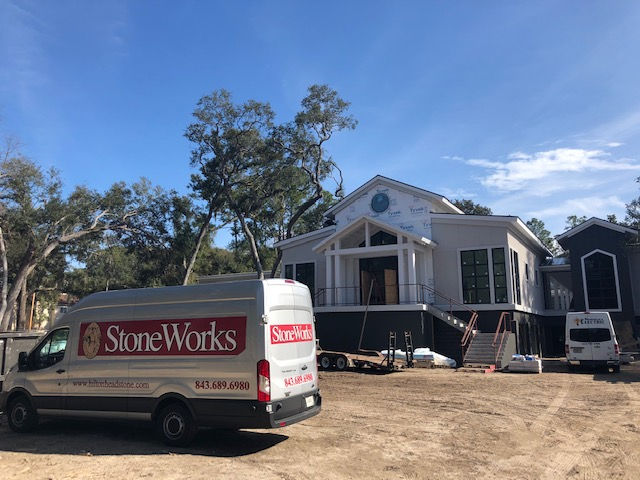
I was very proud to land a sale for countertops and tile surfaces for a large law office complex on Hilton Head a few months back. I visited the site earlier today just to make sure everything went smoothly for the template meeting. While there, I was able to spend some time with Matt Driscoll, our head templater, who has been with StoneWorks for about a decade now.
It’s funny, because I remember working with Matt when I was in the fabrication shop, and Matt worked for a different local company. Matt would deliver wooden stick templates to us for fabrication and later return to pick up the finished tops. Hot glue and wooden strips were pretty much the industry standard at that time, and they are still being used by the majority of stone fabrication shops to create the patterns required for cutting. Our saw operators would spend countless hours lining up the diamond blade from one end of the template to another before finally making the first cut into a stone slab. Then they would have to repeat the process for each and every cut needed. All this was done in hopes that the stone would mostly match the template. The process was painfully slow and not very accurate at all.
Today’s sleek contemporary designs with almost flush overhangs, mitered edging, and no bulky splashes require more advanced methods.
Matt and his process really impressed me with how far along things have progressed!! Inside Matt’s van exists a modern, somewhat plush, mobile office. Sound proofed walls, faux wood flooring, Calacatta quartz desk top, lap top computer, and digital sign printer along with a great air conditioning system really created a sense of professionalism.

A tremendous amount of thought and investment went in to this idea of a mobile digital template office. Years ago, our company identified the templating step as a unique key point of the operation. If the template was incorrect or inaccurate, all work and material further down in the process was wasted. Those types of errors can be very expensive and never fail to create unhappy clients.
Later in the day, I found Matt inside the complex standing over a tripod with a computerized digitizing device called the Pro Liner. He pulled out a stylus connected by a taut metal wire from the Pro Liner and began pin-pointing (beep, beep, beep) all of the critical points of the cabinet, sink, and sheetrock walls. While he rapidly clicked away with his stylus, the view screen of the Pro Liner device lit up with a digital drawing of the countertop area. This took about five minutes for the countertop I witnessed.
The Pro Liner device and tripod were then folded up and off to the van we went.
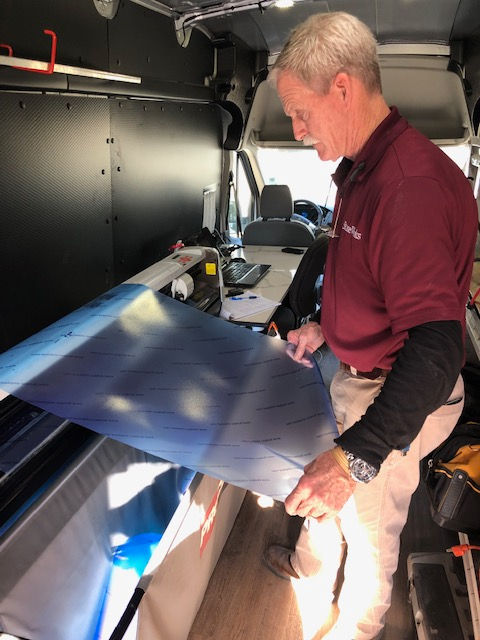
Matt sat at his van’s desk /laptop and used auto CAD software to make minor alterations like needed overhangs, returns, or added faucet holes to the drawing.
Once satisfied with the CAD drawing, the sign printer buzzed to life immediately to Matt’s left. A roll of thin blue mylar plastic was rapidly cut into the exact full-size shape of the needed counter. Amazingly, it even had the actual sink and faucet holes cut so that they could be peeled out by the fabricators. That template was then taken back inside of the jobsite and placed on the cabinet to check for fit. Every little slight bump in the sheetrock and returned area was reflected perfectly by the plastic template – accurate within 1/16 of an inch from what I could tell! This is such a cool process to watch, especially from my standpoint, having been involved with the old methods mentioned above. It’s unbelievable, actually!
So, the funny part is that the fabricators do not necessarily need this physical template anymore. The digital file will be sent via e mail to a network of large CNC (computer numeric controlled) saws and routers. The saws will automatically cut directly from the digital file, not the plastic template. So why is it done?
The purpose of the sign printing method is all about checking for accuracy. If the process is followed correctly, our templaters can leave the jobsite worry free knowing they have created an accurate perfect fitting template.
StoneWorks decided we wanted to employ the very best templaters and invest in the most efficient and accurate systems available to ensure near perfect templates. Today, I am more convinced than ever that we succeeded in doing that! Our clients do recognize the difference.
Yes, templating can be done with less expense using a tape measure and some glue and sticks. We’ve been there, and we would never choose to go back!
Next time you see one of those big silver vans at your jobsite, knock on the back door and say hello to either Matt or Jake. I think you would be truly impressed by what goes on behind the scenes.